Much Asphalt is the largest commercial asphalt
producer in Southern Africa.
We pride ourselves on the consistent quality of our wide range of hot and cold asphalt products, our service offering to all asphalt users large and small, and our excellent safety record.
A New Era Begins
As of Tuesday, April 1, 2025, Much Asphalt officially parted ways with the AECI group, marking the start of a transformative era for the company. Managing director Bennie Greyling praised the dedication of the Much Asphalt team, who worked tirelessly over months to reach this milestone while maintaining their commitment to meeting customer needs.
Bennie Greyling expressed enthusiasm about the company’s future, saying, “We are delighted to welcome our new shareholders, Old Mutual Private Equity and Sphere Holdings. We are committed to ensuring that this partnership delivers value for all involved.
It’s an honour to lead Much Asphalt through this exciting phase, and I’m confident in the unwavering support of our employees as we move forward.”
The ownership transition aligns with a significant milestone for the company—its 60th anniversary. To celebrate this achievement and thank its loyal clients, Much Asphalt plans to host events across South Africa. These gatherings will highlight the company’s enduring “Together We Can” philosophy, which has guided its success for six decades.
6th November 2024
Old Mutual Private Equity (OMPE) and Sphere Investments (Sphere) have announced they have concluded an agreement with Johannesburg Stock Exchange listed AECI Limited to acquire 100% of Much Asphalt alongside the Much Asphalt Management team. The deal is valued at ZAR 1.05 billion and will be financed through a combination of debt and equity. Much Asphalt is South Africa’s largest commercial manufacturer of asphalt products and bituminous binders and emulsions, the latter supplied by SprayPave, a division of Much Asphalt, which are principally used in the road surfacing industry. The company has an unrivalled national footprint, the only player with a nationwide presence which, combined with Much Asphalt’s high levels of service, consistency of supply, reputation and quality of product, further strengthens its offering. OMPE and Sphere believe an investment in the country’s road infrastructure, a key enabler of economic growth and job creation, aligns with the objectives of the Government of National Unity. This, combined with Much Asphalt’s strong competitive offering, means that the company is well-positioned to play a meaningful role in South Africa’s road infrastructure spend over the medium to long term. This transaction marks the first and anchor investment in the newly launched OMPE Fund VI. OMPE and Sphere will partner with the Much Asphalt management team over the investment tenure and through stewardship, capital and perspective, seek to generate transformative growth and business transformation to provide an attractive return to investors and contribute meaningfully to the lives of the employees and communities within which Much Asphalt operates. Jacci Myburgh, Co-Head of OMPE said: “We have confidence in the infrastructure repair initiatives under the new South African Government and actively look to invest behind sectors that we think will recover back to more normal levels over the medium to long term, compared to a volatile and abnormal last ten years for the South African economy. An effective road network is critical to the exciting re-build that is underway in South Africa, which should stimulate economic growth and lead to the creation of new jobs. Burchert Johannes, Investment Principal at OMPE said: “Much Asphalt has a deeply experienced, best-in-class management team. Their experience, technical knowledge and commerciality has seen the company successfully navigate through several industry cycles and we look forward to partnering with them and Sphere to grow the business.” Mohammed Sabi, Director at Sphere, said: “Road infrastructure plays a pivotal role in enabling economic development, connecting South Africans and empowering previously disadvantaged communities in isolated parts of our country. Our investment in Much Asphalt is a continuation of our 21-year track record of investing in high quality business which supply critical goods and services to their customers. We look forward to working with OMPE and the management team to unlock the growth opportunities available to the business in both South Africa and the broader SADC region.” Bennie Greyling, Managing Director of Much Asphalt said: “We have built a solid business that is well-placed to benefit from the catch-up in the road infrastructure spend backlog in the country. We look forward to the next chapter in our business growth through the partnership with Old Mutual Private Equity and Sphere, two highly respected financial investors in the South African landscape.” The transaction is expected to close during the first quarter of 2025, subject to customary regulatory approvals. ABOUT OLD MUTUAL PRIVATE EQUITY Old Mutual Private Equity, part of Old Mutual Alternative Investments, is one of the largest and most established private equity managers in South Africa with a 24-year heritage of being a significant investor in privately owned businesses across key industries and sectors. OMPE has invested in some of South Africa’s strongest private businesses, including Actom, Tourvest, Ti-Auto, Primedia, In2Food and 10x. We have deployed more than R12 billion across 37 transactions, delivering R34 billion in value, including R21.5 billion across 26 exits and R12.4 billion in remaining value. OMPE has also been involved in some of the landmark private equity transactions in South Africa over the years, including some of the largest PE delistings from the Johannesburg Stock Exchange (Pepkor, Consol Glass, Long4Life) and some of the largest PE exits, including the IPO of Life Healthcare. OMPE is currently raising and deploying its sixth fund, OMPE Fund VI. ABOUT SPHERE Established in October 2003, Sphere is a leading Black investment holding company. The cornerstone of Sphere’s approach to making investments is one of partnership: we seek to forge strong alliances and work together with management teams and co-shareholders to build tangible value over the long term. Over its history, Sphere has successfully partnered with the South African subsidiaries of major global multinationals including Babcock International Group PLC, Honeywell International Inc, and Pearson PLC, and assembled a diversified portfolio of exceptional assets in the engineering and infrastructure maintenance, custom software, industrial and education sectors.
12th June 2023
The South African asphalt industry is working hard to reduce its carbon footprint and improve sustainability by using waste materials to provide road surfaces that last longer. AECI Much Asphalt recently completed a successful trial using non-recyclable glass in the asphalt layer. As this concept continues to develop, another potential game-changer is being tested. This time it is Instant Bio-Bitumen, a carbon-negative alternative to conventional bitumen derived from the refining of crude oil for use as the binder in asphalt products. Instant Bio-Bitumen combines asphaltenes extracted from naturally occurring hydrocarbon resins with a maltene component derived from waste cashew nut shells. It can be produced by blending the ingredients or introducing them individually during the asphalt manufacturing process. The bio-bitumen dramatically reduces the SHEQ risks associated with traditional bitumen derived from crude oil, reduces total CO2 emissions in asphalt production, and provides a convenient solution for asphalt production in remote locations. “International bitumen supply has been negatively impacted by the IMO 2020 regulations, which limit Sulphur in fuel oil for ships to 0.50% for marine fuels globally, as well as the international move to green energy. In South Africa, the closing down of refineries and limited capacity of those that remain means asphalt manufacturers must import most of their bitumen requirements,” explains Herman Marais, Director: Plant & Technical at AECI Much Asphalt. “We need new solutions, and the development of alternative binders for flexible pavements that decrease impact on the environment is a significant breakthrough,” he says. Morne Labuschagne, Technical Manager: Bitumen at AECI Much Asphalt, adds that several bio-bitumen products containing few to no petrochemical-derived materials are commercially available internationally. “We decided to investigate Instant Bio-Bitumen for use in South Africa due to its novel recipe and recent success in Europe.” A study at AECI Much Asphalt’s Central Laboratory in Cape Town in 2022 compared the properties of a traditional asphalt mixture manufactured with 50/70 penetration grade bitumen from a local refinery and an asphalt mixture using Instant Bio-Bitumen. According to Labuschagne, the results showed that the properties of the traditional asphalt mixture using the wet blend process were similar but generally inferior to the dry blended asphalt mixture using Instant Bio-Bitumen. In February 2023 a plant trial was conducted at AECI Much Asphalt’s Contermankloof site in the Western Cape but not evaluated in detail due to lower-than-expected binder content. A second trial is planned, with the asphalt mixture to be donated to a primary school for repairs and maintenance to parking areas, walkways and access roads. “We are planning more paving trials on higher volume roads in the Western Cape,” says Labuschagne. “We are also conducting more research using aggregates from different sources and Instant Bio-Bitumen with various asphaltene/maltene ratios. The incorporation of Instant Bio-Bitumen in warm mix asphalt with high ratios of reclaimed asphalt is the next step in our investigations.” AECI Much Asphalt continues to explore alternative sustainable recycling streams for various other waste materials such as foundry sand, waste shock tube generated by the explosives industry, Sulphur by-products and filter cake generated during mineral oil recycling. Watch this space.
17th November 2022
In 2006 AECI Much Asphalt’s Central Laboratory in Cape Town became the first asphalt testing laboratory in South Africa to achieve accreditation from the South African National Accreditation System (SANAS). Cenlab, as it is known, has now taken this significant step further to become the only fully accredited bitumen and asphalt laboratory in South Africa, reports AECI Much Asphalt Managing Director Bennie Greyling. Firyaal Moos, Cenlab Manager, elaborates that all the current specialised testing carried out at the laboratory has been audited and accredited in a step that ensures the facility is 100 per cent covered by SANAS. This includes Dynamic Modulus & Flow, Hamburg Wheel Tracker, Fatigue Life and Dynamic Creep, PG bitumen testing, as well as rubber testing techniques encompassing Dynamic Viscosity, Flow, Compression Recovery, and Ball Penetration & Resilience. Extension of scope “Our Central Laboratory now has SANAS accreditation for all the relevant aggregate, binder and asphalt test methods.” “Cenlab has been SANAS accredited for a large number of test methods for the past 16 years and we have been audited every 18 months since then,” Moos explains. ‘’However, testing methods have developed and changed over the years, and we recently applied for an “Extension of Scope” to include the most recent test methods, as well as others for which we have not previously been accredited. These advanced asphalt and bitumen rubber tests methods were the focus of the latest audit.” She adds that SANAS accreditation begins with assessment of the laboratory systems, including staff, equipment maintenance, calibrations, and verifications, followed by the test methods. Additional test methods can then be included through the “Extension of Scope” process. 14 additional test methods “Since August 2006 Cenlab has been accredited for Marshall Testing, SANS bitumen test methods and SANS aggregate test methods. We included six additional Performance Grade Bitumen test methods in April 2022, and the final eight test methods in October 2022.” While the SANAS Accreditation applies to an AECI Much Asphalt facility, subsidiary AECI SprayPave participates in its correlation testing programmes and Cenlab plays a major role in AECI SprayPave’s binder testing and product development. “We are delighted that Cenlab is now 100% accredited, ensuring that we produce high quality test results which are continuously monitored and analysed through the checks and balances we have in place,” says Moos. “Our daily activities incorporate equipment calibrations and verifications, regular updating of test methods, and continuous staff training. It is essential for us to keep up to date with the latest developments in specifications and testing regimes. Our SANAS accreditation also requires our involvement in both inter- and intra-laboratory comparative testing programmes for all our accredited test methods.” Sustaining relationships She points out that AECI Much Asphalt aims to provide its clients with world class service and the peace of mind of knowing that test results are supported by stringent management systems to ensure quality and conformity. “What Firyaal Moos and her team have achieved is truly remarkable and we are very proud of our flagship laboratory,” says Bennie Greyling.” “AECI Much Asphalt has built strong, lasting industry relationships in the past 50 years and I believe Cenlab’s latest success will help to sustain these relationships.” Moos attributes Cenlab’s long-term success as a SANAS-accredited facility to hard work and dedication, together with the best efforts of her team to keep pace with changes and developments in the industry. “Teamwork is key, and every team member plays a very important part in ensuring overall success.” The Benoni Laboratory in Gauteng has also upgraded significantly in recent years to offer all the most up-to-date testing equipment and techniques and is well on the road to its first SANAS audit. “We are learning from the Cenlab team and will try to emulate their outstanding achievement in the near future,” says Joanne Muller, AECI Much Asphalt Inner Region Technical Manager.
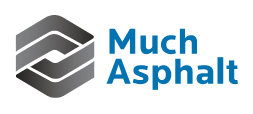

Much Asphalt
is a B-BBEE Level 2 contributor against the Amended Construction Sector Codes in South Africa.
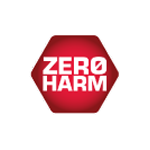
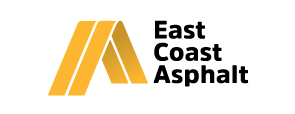
The manufacturing facilities and offices of Much Asphalt, SprayPave and East Coast Asphalt are operating according to the requirements of the South African Government’s Covid-19 health and safety protocols. For information on Covid-19, please follow the link sacoronavirus.co.za.